Guía para principiantes: Sistema de Control Industrial (ICS)
La industria necesita una total seguridad para evitar cualquier circunstancia indeseada. De ahí que surjan los sistemas de control industrial. Se sabe que son procesos definidos que se llevan a cabo para controlar los sistemas industriales a diferentes niveles. A continuación, lee para conocer detalladamente los sistemas de control industrial.
EdrawMax
Software de Diagramas Todo en Uno
¿Qué es el sistema de control industrial?
El sistema de control industrial (ICS) es un término específico utilizado para definir la combinación de software y hardware con la red para equilibrar la infraestructura industrial. Utiliza varias tecnologías, como los controladores lógicos programables (PLC), el control de supervisión y adquisición de datos (SCADA), los sistemas de automatización y control industrial (IACS), las unidades terminales remotas (RTU), los dispositivos electrónicos inteligentes (IED), los dispositivos de control y los sensores.
Por lo tanto, se trata generalmente de un sistema de información utilizado para controlar diferentes procesos industriales como la manipulación de productos, la fabricación, la producción y la distribución. Estos mecanismos incluyen sistemas de adquisición de datos y control de supervisión para gestionar los activos dispersos geográficamente.
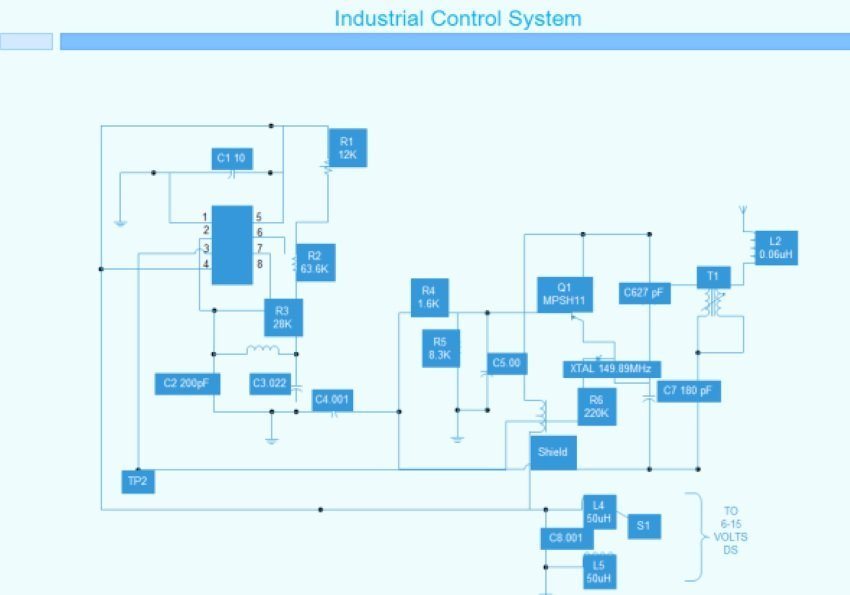
Evolución de los sistemas de control industrial
Inicialmente, se utilizaban paneles locales para controlar las plantas de procesos. Sin embargo, este sistema requería personal. En la siguiente fase de desarrollo, se introdujeron salas de control centralizadas para transmitir todas las mediciones de la planta. Este proceso de centralización tuvo cierto éxito. Pero es inflexible, ya que cada bucle de control tiene su propio hardware de control, que además requiere la reconfiguración de las señales mediante el recableado o la reconducción de las tuberías. Además, el sistema requiere el movimiento continuo del operador, lo que puede suponer una dificultad.
Por lo tanto, se utilizaron procesadores electrónicos para reemplazar estos controladores con algoritmos computacionales. Estos se alojan en racks de entrada y salida junto con sus procesadores de control. Entonces, se realizó una especie de sistema distribuido. La política fue aceptable ya que introdujo el registro automático de eventos, habilitó el manejo sofisticado de alarmas y eliminó la necesidad de documentar físicamente.
Se desarrollaron varias formas de bastidores de control y comercialmente se les dio el nombre de Sistema de Control Distribuido (DCS) para controlar grandes sistemas por muchos fabricantes. Sin embargo, estos sistemas también se sustituyeron por PLCs para utilizar pantallas de control y redes de señales. Primero se adoptó en la industria automotriz, donde el uso de la lógica secuencial era sofisticado. Luego, se introdujo en otras aplicaciones basadas en eventos.
Los sistemas SCADA se pueden encontrar en el uso de diferentes aplicaciones de distribución, como gas natural, energía y tuberías de agua, en las que es necesario recopilar datos remotos mediante enlaces de alta latencia. Por lo general, utilizan RTU (unidades terminales remotas) para transmitir los datos a los centros de control.
De este modo, los SCADA, los PLC o los DCS evolucionaron para gestionar sistemas de bucle abierto o cerrado. El aumento de la velocidad de los procesadores ha permitido aumentar la eficacia de los procesos. En 1993, la industria avanzó hacia la mejora del software de control con un aumento de la estandarización del código. La introducción de la programación orientada a objetos (POO) hizo posible el desarrollo tanto de los PC industriales (IPC) como de los controladores de automatización programables (PAC). Además, ha desencadenado muchos avances eficientes, así como un ahorro de costes, en comparación con los PLC tradicionales.
Las nuevas tecnologías y plataformas han contribuido significativamente a la evolución de los sistemas SCADA y DCS, difuminando aún más las diferencias de definición.
¿Por qué son importantes los sistemas de control industrial?
Objetivos de la utilización del SCI
- El objetivo principal es facilitar las comunicaciones a través de diversos protocolos.
- Entre otros fines se encuentran la automatización de sistemas de energía, la automatización de construcción, la automatización de procesos, entre otros.
- El uso de protocolos garantiza la interoperabilidad entre fabricantes.
Ventajas de los sistemas de control de procesos
- Mayor rendimiento, seguridad y fiabilidad.
- El llamado "air gap" contribuye a incrementar la preocupación por la seguridad.
- También ayuda a mantener unidos los sistemas ciberfísicos como la cuarta revolución industrial, cuando todo se conecta a Internet.
- Gestión electrónica eficiente de tareas.
- Disminuye el derroche de energía con la mejora del rendimiento medioambiental.
Limitaciones de los sistemas de control industrial
A continuación, se presentan varios retos a los que deberás enfrentarte mientras implementas los Sistemas de Control Industrial.
- Debes tener en cuenta muchos factores, como la incertidumbre del proceso, las perturbaciones, la dinámica del proceso y la saturación de los actuadores.
- Los resultados pueden complicarse si se utilizan herramientas computacionales para diseñar un sistema de control.
- Es posible que los errores que se produzcan sean peligrosos o puedan dañar todo el sistema.
Diferentes tipos de sistemas de control industrial
Existen tres tipos de control eléctrico comunes como se indica a continuación.
-
Control de supervisión y adquisición de datos (SCADA)
Los sistemas SCADA sirven para supervisar sitios de campo a larga distancia a través de un mecanismo centralizado. Suelen contener dispositivos como PLCs u otros módulos de hardware comerciales que se distribuyen en varios lugares. En lugar de proporcionar un control total, se sabe que proporcionan una supervisión a nivel de control. Industrias como la de las tuberías, los centros de tratamiento de aguas o la transmisión de energía eléctrica hacen uso de estos sistemas.
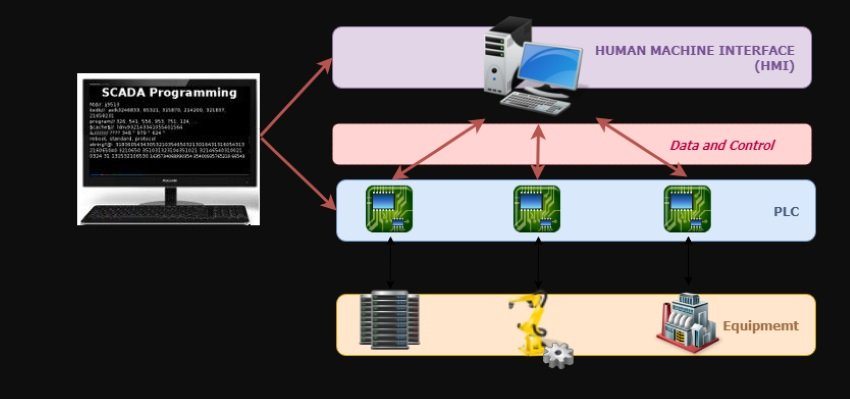
Fuente de la imagen: dpstele.com
-
Sistema de control distribuido (DCS)
Estos sistemas se utilizan para controlar la producción de un lugar. Se mantiene el punto de ajuste deseado para enviarlo al controlador o al actuador que da las instrucciones a las válvulas. Estos datos pueden conservarse para futuras referencias o utilizarse en estrategias de control avanzadas. Cada DCS utiliza un bucle de control de supervisión para gestionar múltiples dispositivos o controladores locales. Además, un DCS es capaz de eliminar el impacto de un solo fallo en todo el sistema.
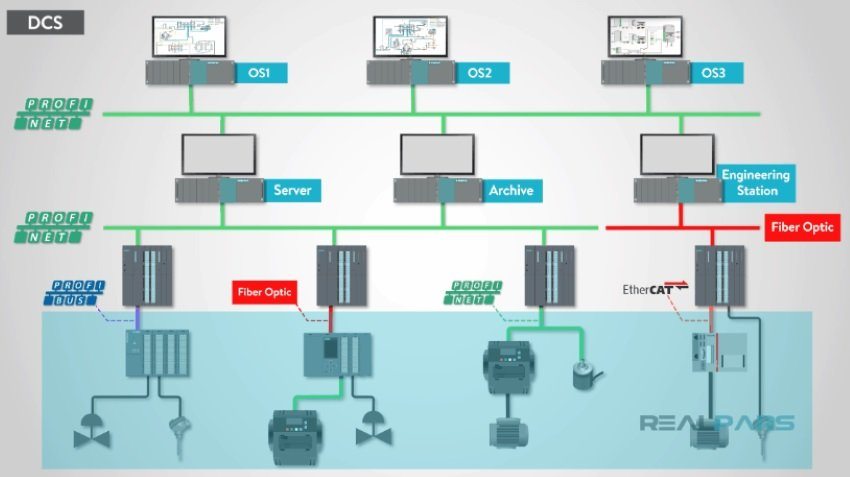
Fuente de la imagen: realpars.com
-
Controladores lógicos programables (PLC)
Los PLC son capaces de realizar diversas aplicaciones industriales con módulos incorporados como la fuente de alimentación, la CPU, los módulos de E/S y otros módulos de comunicación. Los PLC pueden ser integrados o modulares. Un PLC modular es compacto y fijo con funciones de E/S limitadas, mientras que el PLC integrado amplía los módulos de E/S en función de sus características. El módulo de entrada se conecta con los sensores, mientras que los actuadores u otros dispositivos de salida se conectan con el módulo de salida.
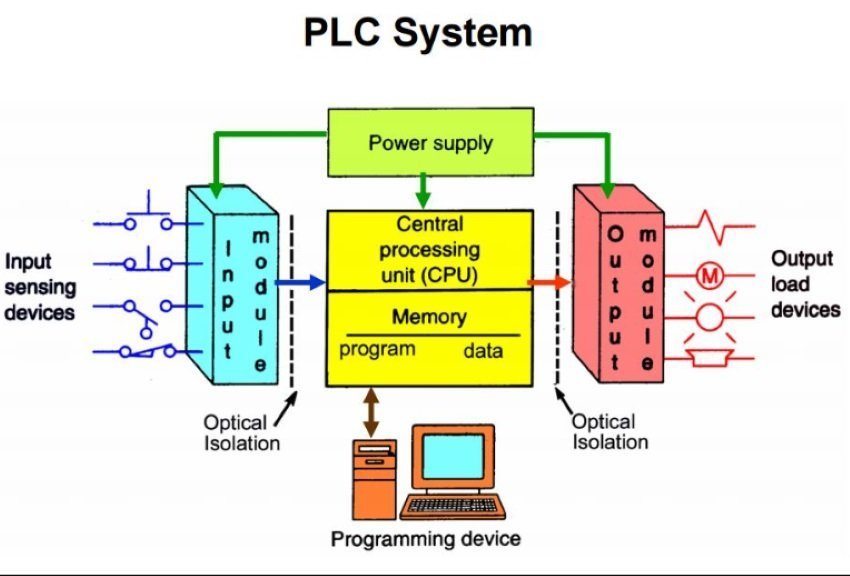
Aplicaciones de los sistemas de control industrial - Aprende con ejemplos
A continuación, se presentan tres ejemplos prácticos de Sistemas de Control Industrial. Te ayudarán a entender mejor el concepto.
El PID es un controlador muy utilizado en ICS, y el diagrama que se presenta a continuación muestra cómo se controla. Se aplica automáticamente a la corrección sensible y precisa a la función de control. Se puede describir la respuesta del controlador de manera efectiva en términos de su capacidad de respuesta al error.
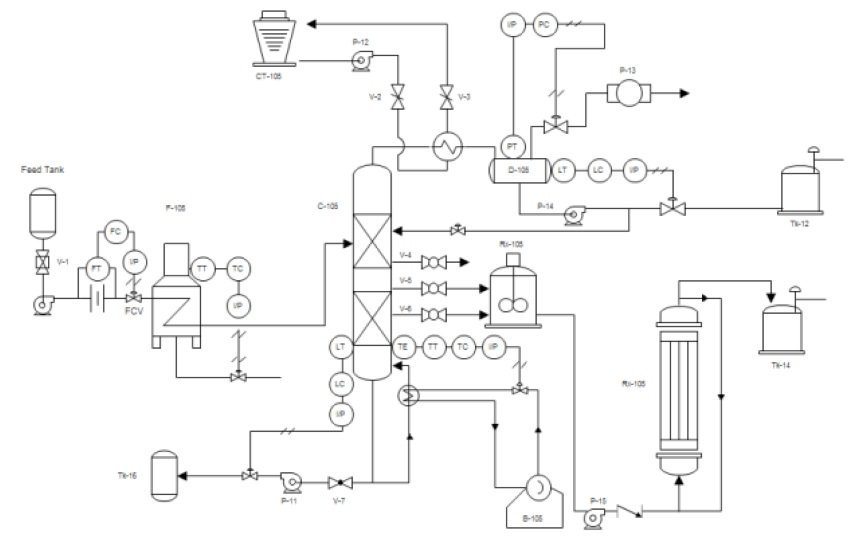
Se trata de un ejemplo de respuesta de tres vías, uno de los controladores utilizados en el ICS. El diagrama es sencillo y utiliza varios símbolos para indicar el proceso.
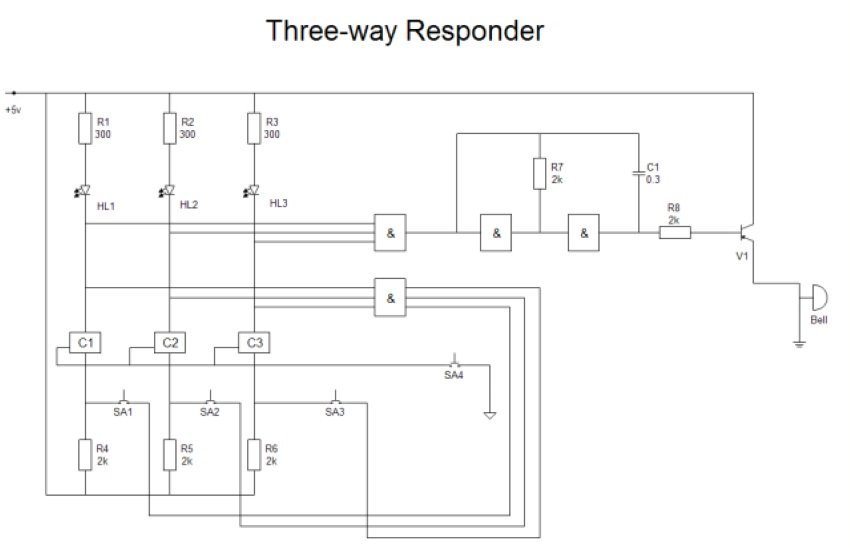
El ejemplo del PID de producción es un sistema de control de procesos. Aunque parece algo complicado, el uso de diferentes símbolos y formas hace que sea cómodo de leer.
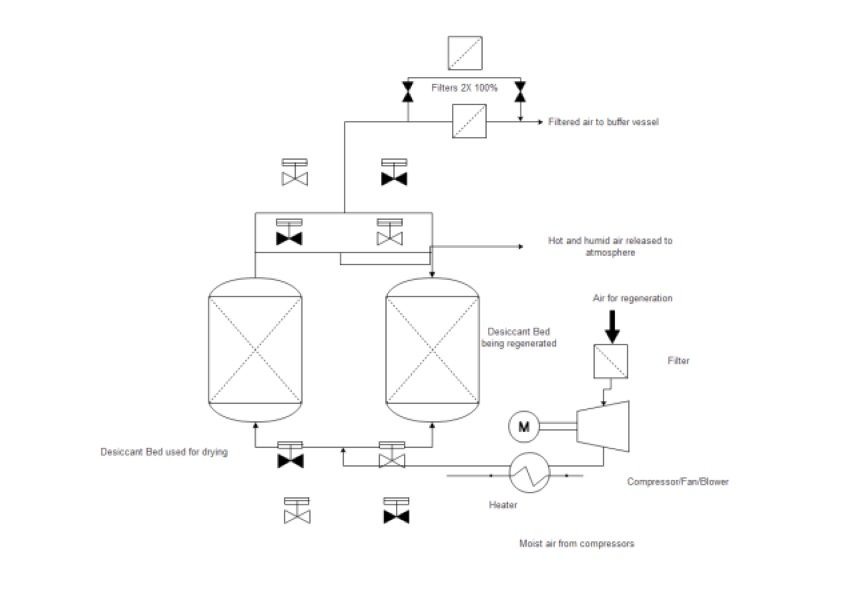
¿Cómo crear un Diagrama de Sistema de Control Industrial con Edraw Max Online?
Edraw Max Online es una poderosa herramienta para dibujar Sistemas de Control Industrial. Las plantillas están disponibles de forma gratuita, puedes tener hasta tres proyectos. Una ventaja significativa de esta herramienta es su disponibilidad en línea y su amplia gama de funciones.
Es un software completo, sencillo y profesional. Incluye organigramas, diagramas de flujo, presentaciones empresariales, diagramas de red, mapas mentales, planos de edificios, ilustraciones científicas, diagramas UML, diseños de moda, estructuras de programas, diagramas de ingeniería eléctrica, diagramas de diseño web, diagramas de bases de datos, gráficos direccionales y mucho más.
Los aspectos para considerar antes de realizar los diagramas de sistema de control industrial son:
- Conocer el tipo específico que se quiere crear.
- Aprender los diferentes símbolos y formas relacionadas con el diagrama.
- Considerar los requisitos de la industria a partir del análisis de los diferentes tipos de ICS.
A continuación, expliquemos los pasos para crear un diagrama de Sistemas de Control Industrial con Edraw Max Online
Ve a Edraw Max Online. Haz clic en Regístrate y crea una cuenta para tener acceso a varias plantillas.
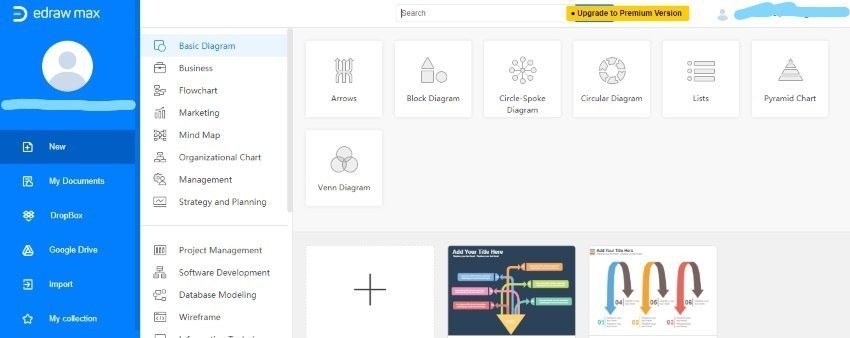
Para abrir el ICS, deberás hacer clic en Ingeniería Industrial en la barra de menú lateral. Esta opción mostrará varios diagramas, como el PID de proceso, el PID de generación de servicios públicos, el PID ambiental, el PID de distribución y el PID de sistemas auxiliares.
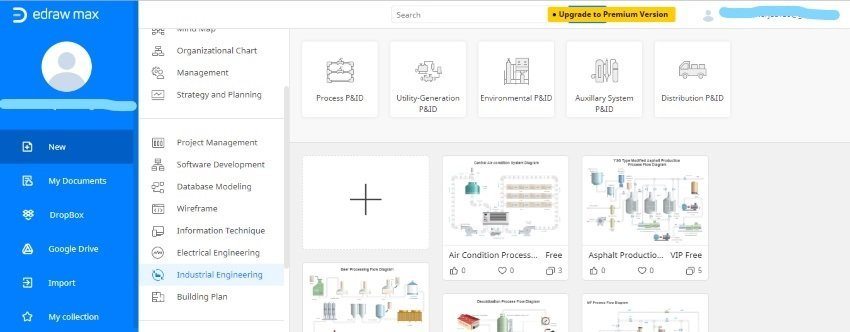
Puedes seleccionar el que necesites y empezar a crear el gráfico del sistema de control de procesos.
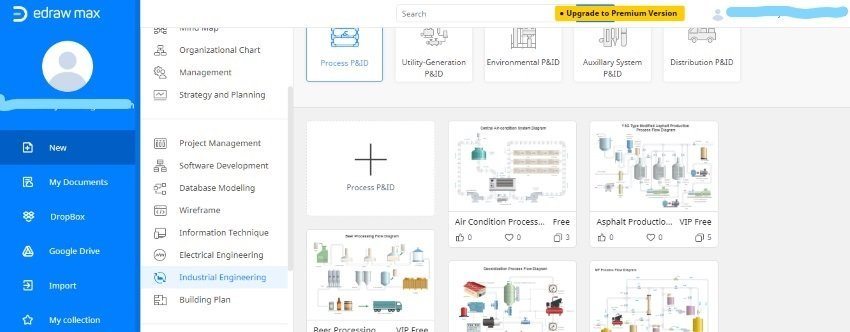
El sistema de control industrial en el futuro
Como sistema seguro para la producción industrial, el control eléctrico suele adoptar nuevas tecnologías desarrolladas para mejorar el sistema industrial global. Las empresas tienden a seguir procesos de control para requisitos y aplicaciones específicas. En el futuro, los sistemas basados en computadores serán la base de todas las necesidades industriales. Ya sea basado en una estructura jerárquica o genérica, el sistema de control industrial se aplica a todo tipo de industrias.
Además, implica el uso de máquinas inteligentes en las plantas industriales para garantizar que todos los procesos se completen en el menor tiempo posible. Para ello, se necesitan diferentes sistemas de control que faciliten el funcionamiento de los equipos y ejecuten todas las tareas asignadas con la precisión, velocidad y resistencia adecuadas. Esto se puede conseguir a través de las diversas técnicas mencionadas y será de esta forma hasta no existan preocupaciones por cualquier evento no deseado.